Sektor produkcyjny należy do najbardziej dynamicznych branż. Obecnie nieustannie dąży się do zwiększenia ogólnej precyzji i dokładności, a procesy takie jak drutowe EDM, które zapewniają dokładnie to, są niczym innym, jak transformacją dla branży.
Czym więc dokładnie jest Wire EDM i dlaczego uważa się ją za przełomową dla sektora produkcyjnego? Poniższy tekst przyjrzy się podstawom tej zaawansowanej techniki produkcyjnej z zastosowaniami w różnych branżach.
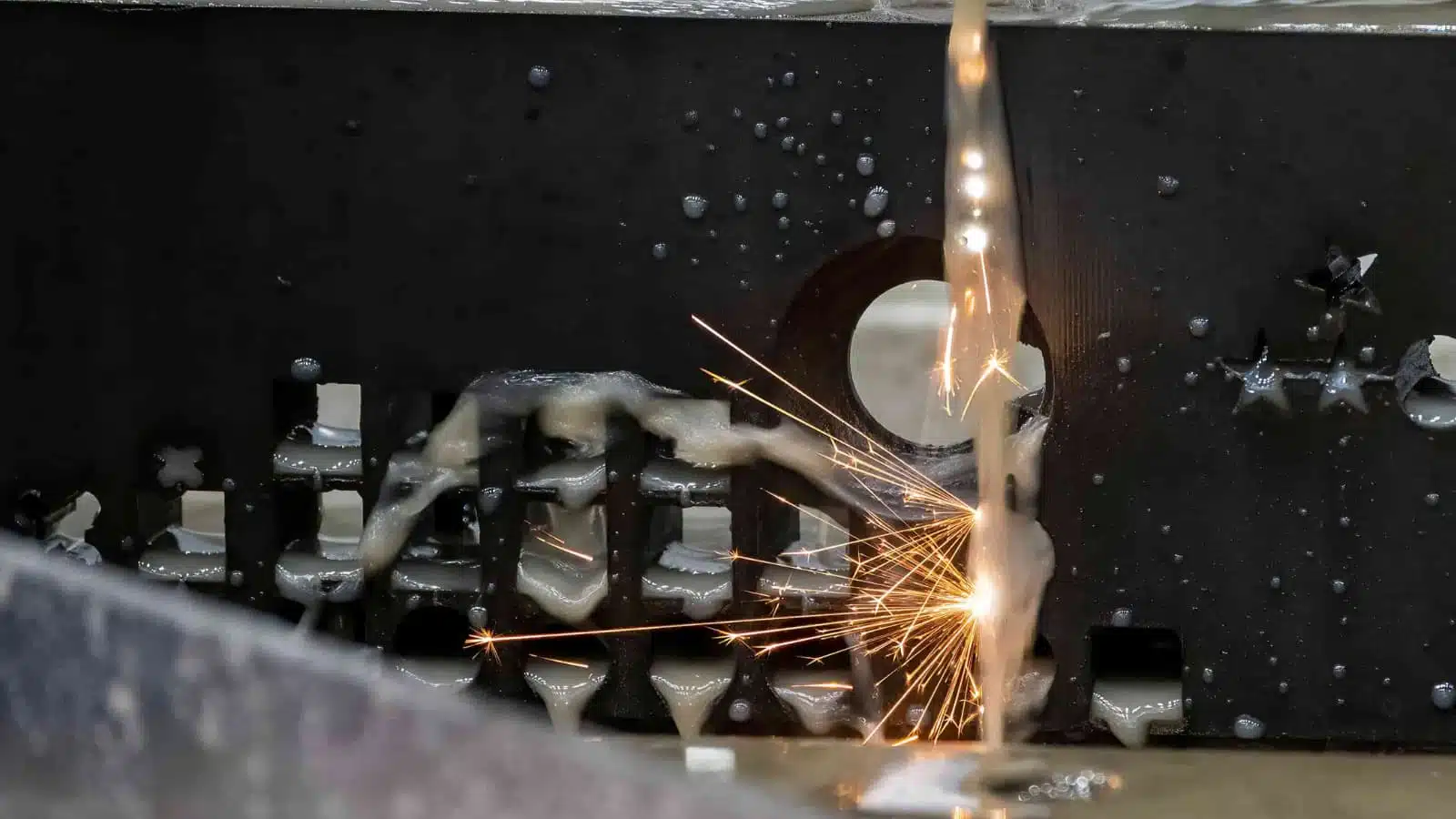
Krótkie wprowadzenie do obróbki elektroerozyjnej drutem
Obróbka elektroerozyjna drutem (EDM) została zapoczątkowana w latach 40. XX wieku przez dwóch radzieckich naukowców, którzy jako pierwsi erozję metalu za pomocą wyładowania elektrycznego. Technologia ta odnotowała znaczny postęp w latach 60. i 80. XX wieku, stając się bardziej rozpowszechniona komercyjnie w produkcji. Pod koniec lat 90. XX wieku, dzięki udoskonaleniom IT i CNC, maszyny do obróbki elektroerozyjnej drutem stały się bardziej skomputeryzowane, zwiększając ich wydajność i precyzję.
Obecnie obróbka elektroerozyjna drutowa jest niezbędna w takich gałęziach przemysłu jak lotnictwo, motoryzacja i medycyna, słynących z możliwości tworzenia skomplikowanych projektów i złożonych kształtów, których nie da się osiągnąć za pomocą tradycyjnych metod obróbki.
Proces obróbki elektroerozyjnej drutem
Obróbka elektroerozyjna drutem (EDM) to precyzyjna metoda, która wykorzystuje kontrolowane iskry elektryczne do topienia maleńkich części przedmiotu obrabianego. Elektroda drutowa, zwykle wykonana z mosiądzu lub materiałów ocynkowanych, wytwarza tę iskrę i porusza się po ustalonej ścieżce. Jej zaleta? Działa bez kontaktu fizycznego, zapobiegając uszkodzeniom lub śladom zarówno na przedmiocie obrabianym, jak i na narzędziu.
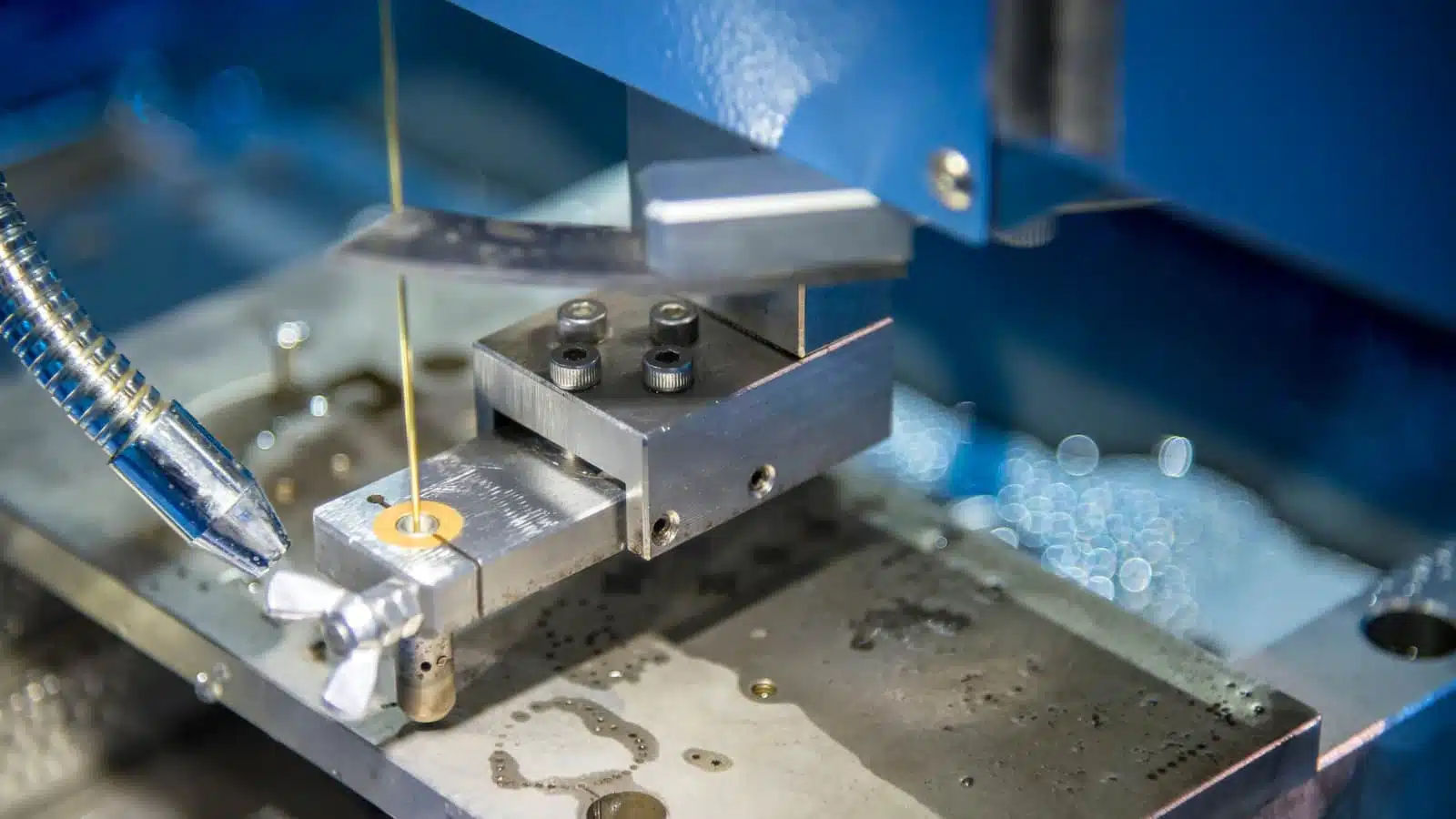
Jak działa EDM
EDM opiera się na energii cieplnej z wyładowania elektrycznego. Wyładowanie to podgrzewa obrabiany przedmiot do temperatury topnienia, tworząc maleńkie kanały plazmowe. Kanały te, często wielkości mikrometrów, mogą szybko zniknąć.
Proces EDM odbywa się w medium dielektrycznym, zwykle w wodzie dejonizowanej. Płyn ten chłodzi obrabiany przedmiot i usuwa odparowany materiał, wspomagając ciągłą obróbkę.
Znaczenie elektrody drutowej
Działając zarówno jako przecinak, jak i przewodnik, drut elektrodowy jest niezbędny. Pokryty materiałami takimi jak mosiądz lub cynk, jest odporny na reakcje w wysokich temperaturach. Sterowany przez komputer, zapewnia dokładne cięcia z minimalnym zniekształceniem i wysoką precyzją.
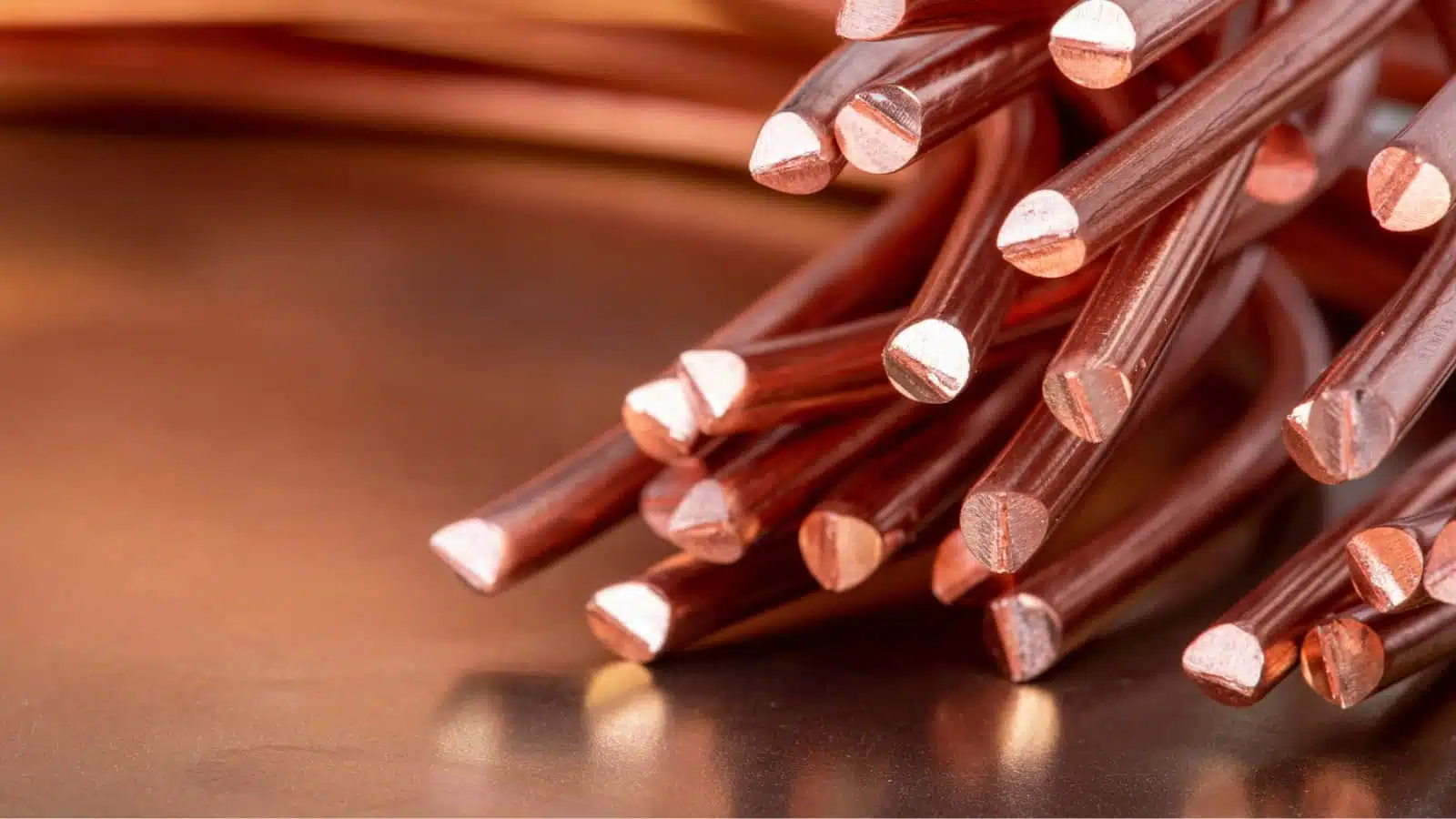
Tolerancje dla obróbki elektroerozyjnej drutem
Cięcie drutem należy do najdokładniejszych procesów produkcyjnych. Dlatego ścisłe tolerancje nie są dla niego czymś niezwykłym. Rzeczywista tolerancja zależy od kilku czynników, w tym zawiłości projektu, możliwości obróbki i umiejętności operatora.
Jednakże standardy i dopuszczalne tolerancje stanowią punkt odniesienia w branży, którego przestrzega wielu producentów.
Tolerancja standardowa i tolerancja drobna
Tolerancja standardowa
Tolerancje liniowe: Zwykle mieszczą się w przedziale od ±0,005 do ±0,001 cala (od 0,127 do 0,0254 mm), wskazując dopuszczalne odchylenie dla takich elementów jak otwory, szczeliny lub profile.
Tolerancja średnicy otworu: Zwykle od ±0,0005 do ±0,001 cala (od 0,0127 do 0,0254 mm), co zapewnia, że obrobione otwory pozostaną w zdefiniowanej średnicy.
Dokładna tolerancja
Tolerancje liniowe: osiągają precyzję na poziomie mikronów, zwykle w zakresie od ±0,0002 do ±0,0001 cala (od 0,0051 do 0,00254 mm), co jest niezwykle istotne w zastosowaniach wymagających najwyższej dokładności.
Tolerancja średnicy otworu: od ±0,0001 do ±0,00005 cala (od 0,00254 do 0,00127 mm), co podkreśla wyjątkową precyzję obróbki elektroerozyjnej drutowej.
Czynniki wpływające na tolerancje w obróbce elektroerozyjnej drutem
Wire EDM słynie z precyzji na poziomie mikronów, co czyni go idealnym do skomplikowanych zastosowań. Jednak jego precyzja nie jest stała i zależy od kilku czynników:
•Stabilność maszyny: Stabilna maszyna zapewnia większą precyzję cięcia.
•Jakość i średnica drutu: Czystość, średnica i cechy elektryczne wpływają na proces obróbki. Optymalne wyniki wymagają równowagi między jakością drutu a średnicą.
• Materiał obrabiany: Mimo że niektóre materiały są łatwiej dostępne dla maszyn, ich wybór musi być zgodny z potrzebami danego zastosowania.
•Warunki płukania: Przepływ medium dielektrycznego ma wpływ na jakość procesu obróbki, wspomaga usuwanie materiału, zapewnia równomierne wyładowania elektryczne i skuteczne odprowadzanie ciepła.
•Kalibracja i konserwacja maszyny: Możliwości maszyny są kluczowe. Doskonałe maszyny z doświadczonymi operatorami są niezbędne do osiągnięcia najlepszych tolerancji.
•Stabilność termiczna: Aby utrzymać znaną precyzję Wire EDM, kontrolowane łuki elektryczne są kluczowe. Niestabilność termiczna może zagrozić dokładności, podkreślając znaczenie stałych warunków.
Najbardziej odpowiednie materiały do cięcia drutem
Metale żelazne
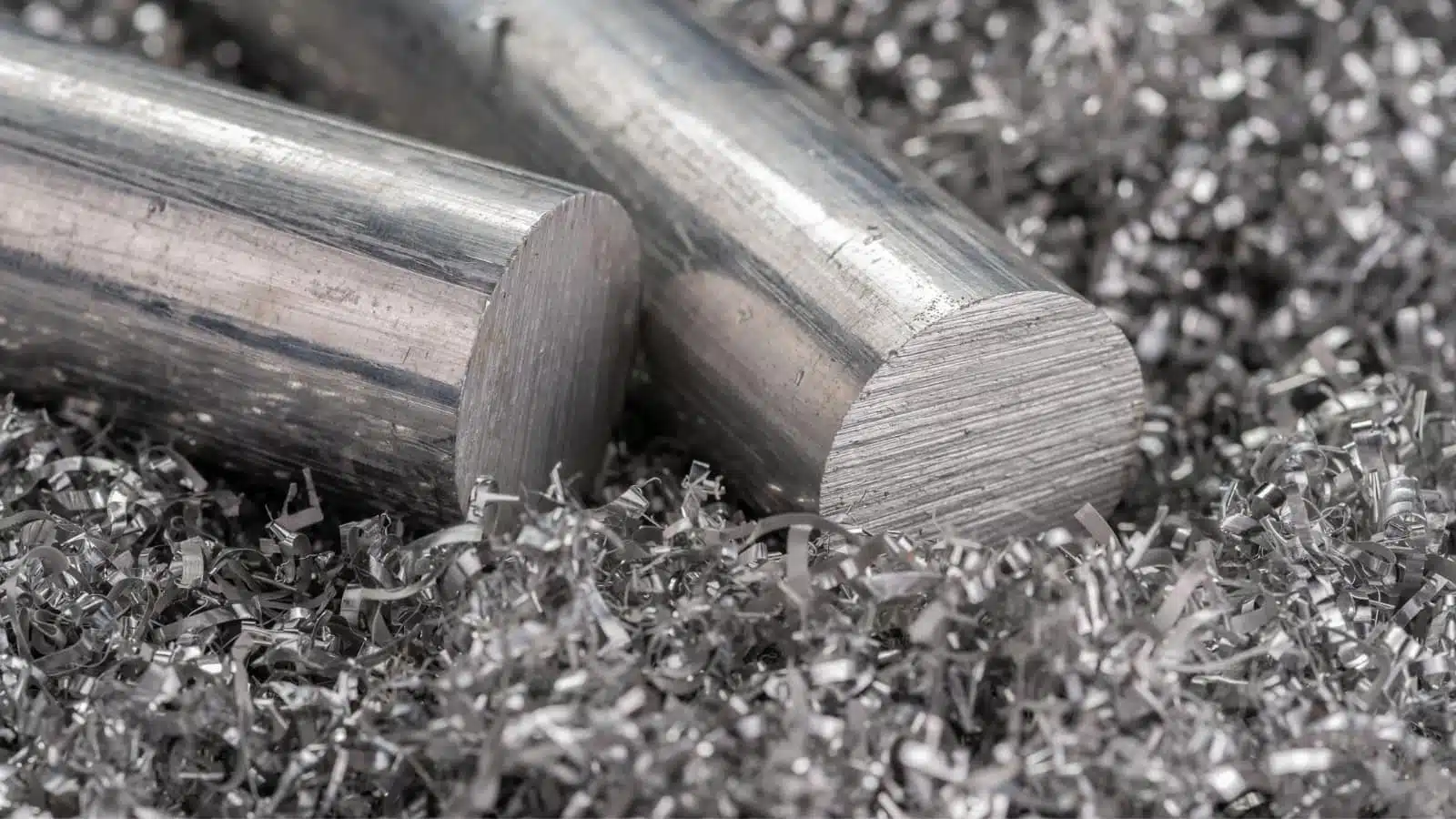
Stal nierdzewna
Łączy trwałość z doskonałą przewodnością elektryczną. Jego zdolność do odporności na korozję sprawia, że jest to poszukiwany materiał w różnych gałęziach przemysłu. W kontekście obróbki wyróżnia się jego zgodność z precyzyjnymi i szczegółowymi projektami.
Stal narzędziowa
Znana ze swoich hartowanych właściwości stal narzędziowa jest podstawą wielu ciężkich narzędzi i precyzyjnych części. Jej wrodzona wytrzymałość w połączeniu z właściwościami elektrycznymi sprawia, że jest ona doskonałym kandydatem do misternych detali i długotrwałej ostrości.
Stal węglowa
Wszechstronny gracz w dziedzinie metali, stal węglowa, choć mniej obrabialna niż jej odpowiedniki, może być dostosowana do perfekcji dzięki odpowiednim wyborom elektrod i parametrom operacyjnym. Jej przystępna cena w połączeniu z wydajnością sprawia, że jest podstawą w wielu branżach.
Stal stopowa
Połączenie elementów, wydajność stali stopowej jest gobelinem jej składników. W zależności od unikalnej mieszanki może oferować wytrzymałość, trwałość i obrabialność, co czyni ją dynamicznym wyborem do różnych zastosowań.
Metale nieżelazne
Tytan
Często nazywany „metalem ery kosmicznej”, tytan ze względu na swoją wytrzymałość i wysoką temperaturę topnienia stwarza wyzwania w konwencjonalnej obróbce. Jednak po wykuciu precyzyjnymi narzędziami odsłania skomplikowane i wytrzymałe projekty, co czyni go ulubionym materiałem dla przemysłu lotniczego i medycznego.
Aluminium
Ulubieniec lekkich metali, aluminium, jest ceniony za swoją wspaniałą przewodność elektryczną i ciągliwość. Nie tylko oferuje łatwość obróbki, ale także obiecuje wytrzymałość bez ciężaru, co czyni go kluczowym w branżach od transportu po pakowanie.
Miedź
Miedź, przewodnik par excellence, jest sercem wielu cudów elektrycznych i elektronicznych. Jej naturalny czerwono-pomarańczowy odcień w połączeniu z możliwością formowania w szczegółowe komponenty sprawia, że jest niezastąpiona we wszystkim, od elektroniki po sztukę dekoracyjną.
Mosiądz i brąz
Te stopy, lśniące w swoich złotych odcieniach, nie są tylko kwestią estetyki. Ich godne pochwały właściwości elektryczne sprawiają, że są to materiały do komponentów, w których precyzja spotyka się z pięknem, na przykład w ozdobnej biżuterii lub precyzyjnie wykonanych częściach elektronicznych.
Kluczowe zastosowania obróbki elektroerozyjnej drutem w nowoczesnej inżynierii
Obróbka drutowa EDM zyskuje na popularności ze względu na swoją wszechstronność w obsłudze różnych materiałów i zdolność do osiągania precyzyjnych detali i ścisłych tolerancji, co czyni ją kluczową w nowoczesnej produkcji. Oto trzy główne zastosowania:
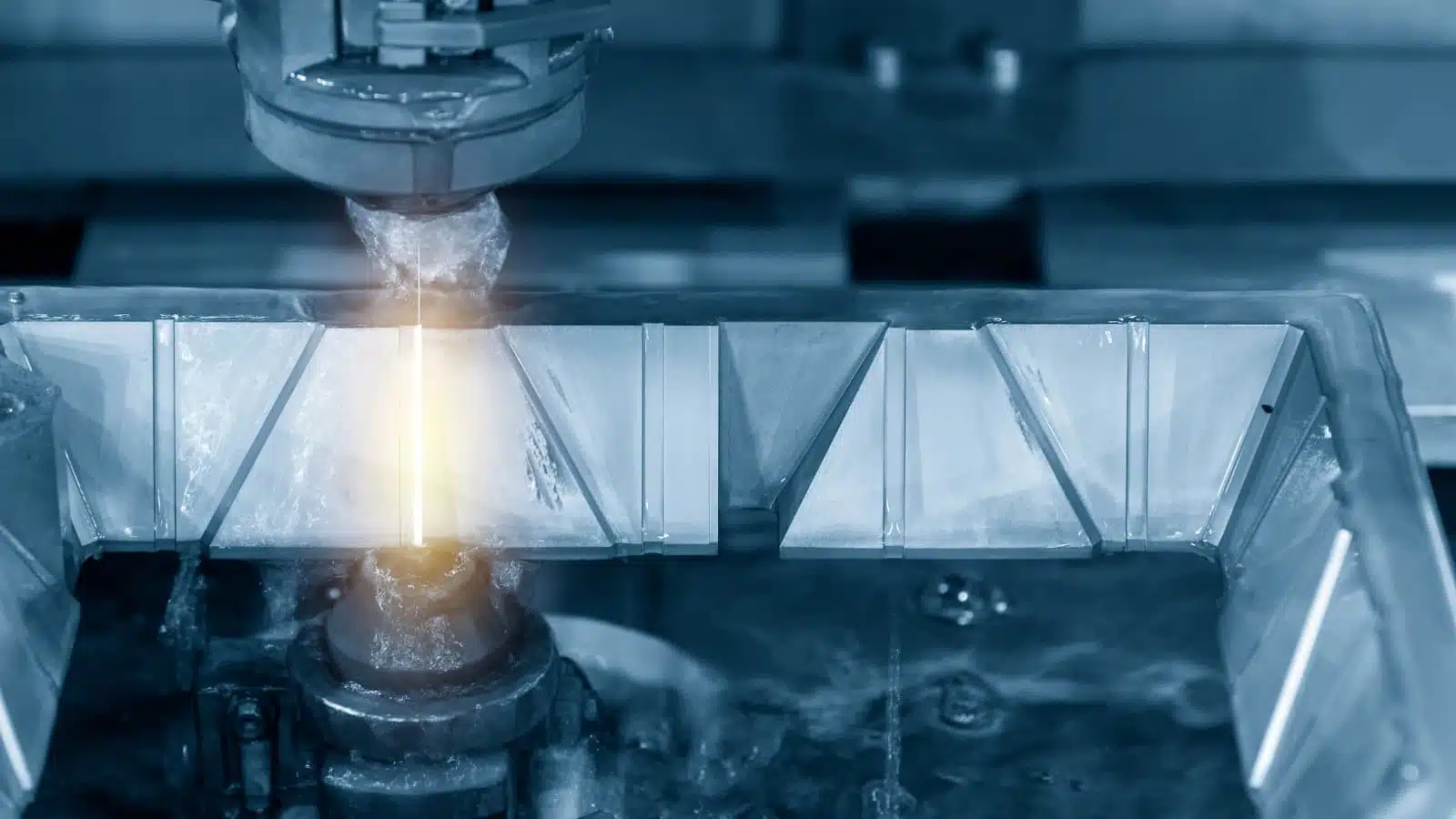
Produkcja części precyzyjnych
Popularny wybór do produkcji precyzyjnych części o ścisłych tolerancjach. Doskonale nadaje się do produkcji skomplikowanych kształtów, drobnych detali i małych cech w różnych materiałach.
Branże takie jak lotnictwo, medycyna, motoryzacja i elektronika wykorzystują obróbkę elektroerozyjną drutową do tworzenia kluczowych komponentów, w tym kół zębatych, dysz, złączy i skomplikowanych form.
Produkcja narzędzi i matryc
Drut EDM jest narzędziem do kucia form, matryc i specjalistycznych narzędzi, obsługującym procesy od formowania wtryskowego do tłoczenia. Zdolność tej metody do utrzymywania dokładnych wymiarów i rzeźbienia ostrych kątów zapewnia najwyższą jakość i jednorodność w produkcji na dużą skalę.
Rozwój prototypu
W celu szybkiego i precyzyjnego prototypowania inżynierowie i innowatorzy skłaniają się ku Wire EDM. Przyspiesza to walidację projektu i rygorystyczne fazy testowania.
Prototypy wycinane metodą obróbki elektroerozyjnej są wiernym odzwierciedleniem produktu końcowego, co podkreśla jego znaczenie w cyklu ewolucji produktu.
Biorąc pod uwagę mocne strony technologii Wire EDM w tych kluczowych obszarach, jej precyzyjne i dokładne możliwości są szeroko wykorzystywane w wielu branżach.
•Produkcja urządzeń medycznych
•Elektronika i mikrokomponenty
•Lotnictwo i kosmonautyka
•Biżuteria i zegarmistrzostwo
•Branża motoryzacyjna
•Sektor energetyczny
• Naprawa form i matryc
Czas publikacji: 12-12-2023