Precyzyjne części metalowe są często produkowane przy użyciu różnych technologii precyzyjnej obróbki, przy czym powszechną metodą jest obróbka CNC. Zazwyczaj precyzyjne części wymagają wysokich standardów zarówno pod względem wymiarów, jak i wyglądu.
Dlatego przy stosowaniu obróbki CNC metali, takich jak aluminium i miedź, występowanie śladów i linii narzędzi na powierzchni gotowego produktu jest problemem. W tym artykule omówiono przyczyny powstawania śladów i linii narzędzi podczas obróbki wyrobów metalowych. Proponujemy również potencjalne rozwiązania.
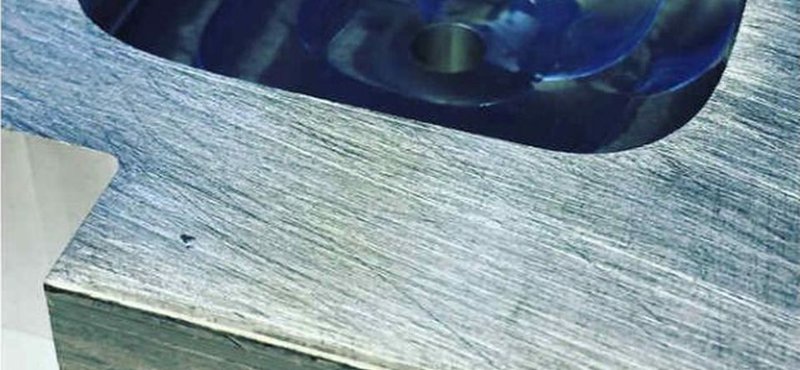
Niewystarczająca siła zacisku osprzętu
Powoduje:Niektóre wyroby metalowe z wnękami wymagają stosowania urządzeń podciśnieniowych i mogą mieć trudności z wygenerowaniem odpowiedniego ssania ze względu na obecność nierówności na powierzchni, co może skutkować powstawaniem śladów lub linii po narzędziach.
Rozwiązanie:Aby temu zaradzić, rozważ przejście z prostego ssania próżniowego na ssanie próżniowe połączone z ciśnieniem lub wsparciem bocznym. Alternatywnie, zbadaj alternatywne opcje mocowania oparte na konkretnych strukturach części, dostosowując rozwiązanie do konkretnego problemu.
Czynniki związane z procesem
Powoduje:Niektóre procesy produkcyjne mogą przyczyniać się do tego problemu. Na przykład produkty takie jak tylne obudowy tabletów PC przechodzą sekwencję etapów obróbki, obejmującą wykrawanie otworów bocznych, a następnie frezowanie krawędzi CNC. Ta sekwencja może prowadzić do widocznych śladów narzędzi, gdy frezowanie dociera do pozycji otworów bocznych.
Rozwiązanie:Częstym przypadkiem tego problemu jest wybranie stopu aluminium do obudowy produktu elektronicznego. Aby go rozwiązać, proces można zmodyfikować, zastępując boczne dziurkowanie i frezowanie wyłącznie frezowaniem CNC. Jednocześnie zapewniając stałe zaangażowanie narzędzia i redukując nierównomierne cięcie podczas frezowania.
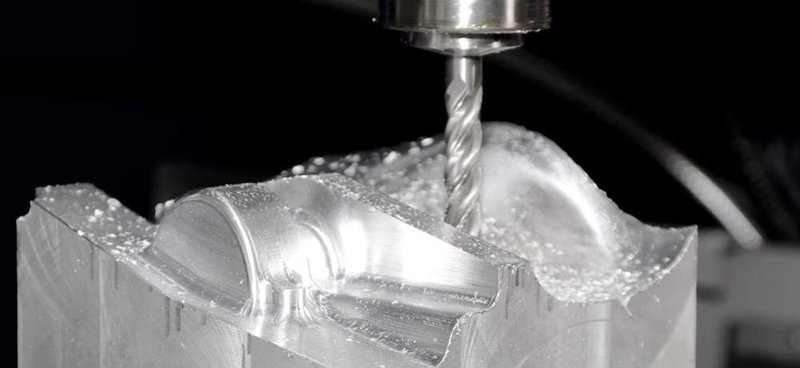
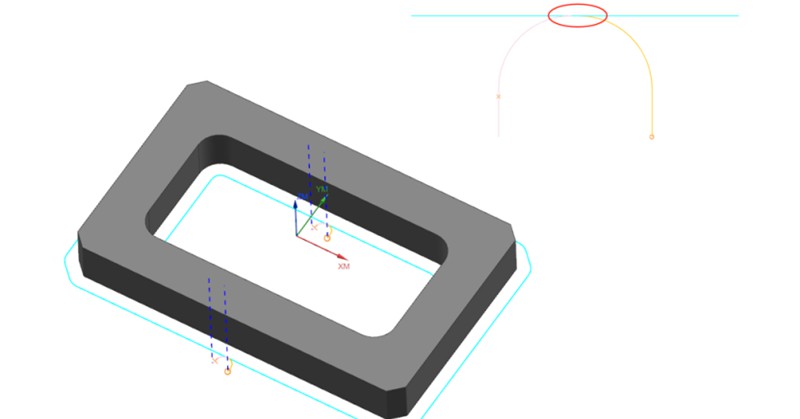
Niewystarczające programowanie zaangażowania ścieżki narzędzia
Powoduje:Ten problem często pojawia się w fazie obróbki konturów 2D podczas produkcji produktu. Źle zaprojektowane zaangażowanie ścieżki narzędzia w programie CNC, pozostawiające ślady w punktach wejścia i wyjścia narzędzia.
Rozwiązanie:Aby sprostać wyzwaniu unikania śladów narzędzi w punktach wejścia i wyjścia, typowe podejście polega na wprowadzeniu niewielkiego nakładania się odległości zaangażowania narzędzia (około 0,2 mm). Ta technika służy do obejścia potencjalnych niedokładności w precyzji śruby pociągowej maszyny.
Chociaż ta strategia skutecznie zapobiega powstawaniu śladów narzędzi, powoduje ona element powtarzalnej obróbki, gdy materiał produktu jest miękkim metalem. W związku z tym ta sekcja może wykazywać różnice w teksturze i kolorze w porównaniu z innymi obszarami.
Wzory łusek ryb na płaskich powierzchniach obrabianych maszynowo
Powoduje:Łuski rybie lub wzory kołowe pojawiające się na płaskich powierzchniach produktu. Narzędzia tnące używane do obróbki miękkich metali, takich jak aluminium/miedź, to zazwyczaj frezy do materiałów stopowych z 3 do 4 rowkami. Mają twardość od HRC55 do HRC65. Te narzędzia tnące są wykonywane przy użyciu dolnej krawędzi narzędzia, a powierzchnia części może wytworzyć charakterystyczne wzory łusek rybie, wpływające na jej ogólny wygląd.
Rozwiązanie:Często obserwowane w produktach o wysokich wymaganiach płaskości i płaskich powierzchniach z zagłębionymi strukturami. Rozwiązaniem jest przejście na narzędzia tnące wykonane z syntetycznego materiału diamentowego, co pomaga uzyskać gładsze wykończenie powierzchni.
Starzenie się i zużycie elementów wyposażenia
Powoduje:Ślady narzędzi na powierzchni produktu są przypisywane starzeniu się i zużyciu wrzeciona, łożysk i śruby pociągowej urządzenia. Ponadto nieodpowiednie parametry luzu systemu CNC przyczyniają się do wyraźnych śladów narzędzi, szczególnie podczas obróbki zaokrąglonych narożników.
Rozwiązanie:Problemy te wynikają z czynników związanych ze sprzętem i można je rozwiązać poprzez ukierunkowaną konserwację i wymianę.
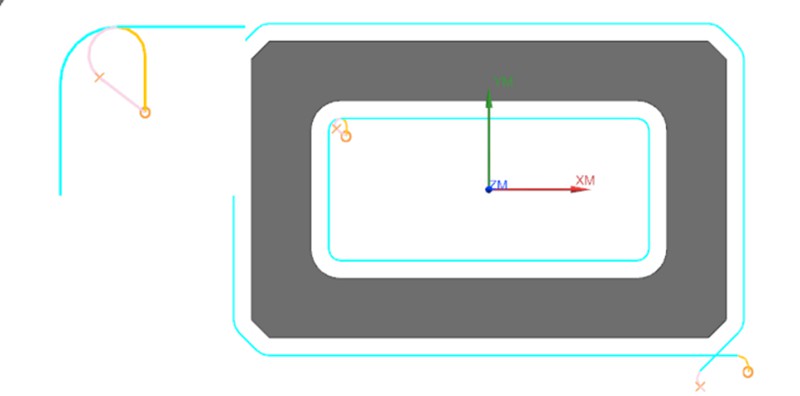
Wniosek
Osiągnięcie idealnej powierzchni w obróbce metali CNC wymaga przydatnych podejść. Istnieją różne metody unikania śladów i linii narzędzi, które obejmują kombinację konserwacji sprzętu, udoskonaleń osprzętu, regulacji procesu i udoskonaleń programowania. Poprzez zrozumienie i skorygowanie tych czynników producenci mogą zapewnić, że precyzyjne komponenty nie tylko spełniają kryteria wymiarowe, ale także wykazują pożądane właściwości estetyczne.